Yesterday, Tesla stock closed at a price per share of $188.18, and while that’s down from the company’s 52-week high of $299.19, it still makes Tesla more valuable than the next four most valuable car companies combined – Toyota, Porsche, Mercedes-Benz and BYD. But it wasn’t always that way. When I started at Tesla as employee number 350 in November, 2009, the company was seriously struggling financially. We were living hand to mouth, which is not unexpected from a small start-up. Still, despite our size, we were ambitious. We had just started the design phase of the Model S and we had high hopes for the car, but a low budget.
It may sound surprising today, but Tesla didn’t have billions in the bank back then, and developing a new car is a very expensive proposition. It takes hundreds of millions of dollars to design, develop, and tool up a new vehicle. Just to give perspective, when Ford developed the new Taurus in 1986, it spent $2 Billion. 25 years later, the costs had only gone up from there.
So at Tesla, we had to get creative to save money wherever we could. You can see the effects of this in the chassis, especially in the steering system and rear suspension.
Here’s a video where I explain all of this:
Steering Racks Are Absurdly Expensive
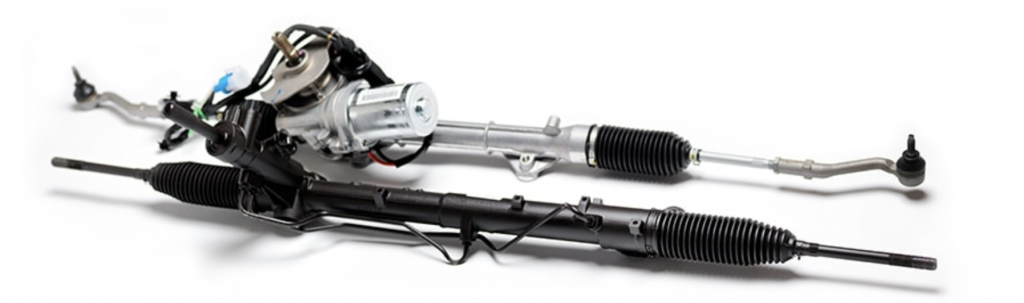
One of the most expensive parts of a car’s suspension system is the steering gear. Designing and tooling a new steering gear can cost well over a $1,000,000. The housing is a complex casting, and the rack bar (an example of which is shown below) is a very complicated forging requiring some very fancy tooling to create the teeth and the helical groove for the electric power assist system.
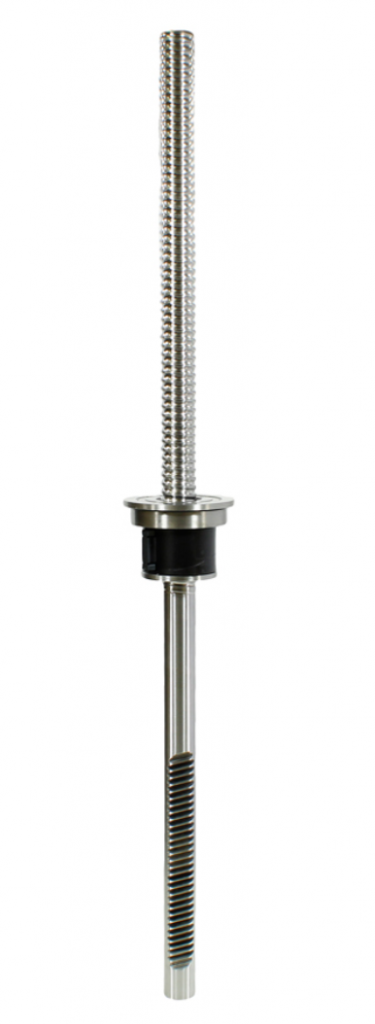
Even in the old days of hydraulic steering systems, steering gears were expensive to make. There was no way a small start-up company like Tesla would be able to afford such a large bill. On top of that, Tesla was an unproven company. We did not have a long history of profitability and success yet. For many traditional suppliers, agreeing to design and develop something as complex and expensive as a steering gear would have been a major risk they were unwilling to take.
The way around that is to find a steering gear that already exists which the supplier and the current owner will agree to let you use. If you’re lucky, you could find a steering gear that fits perfectly, and where the supplier has enough additional production capacity to support your needs. Production capacity was unlikely to be a problem for most suppliers since, at the time, we were only expecting to sell about 20,000 Model S’s per year. But finding just the right gear was going to be a difficult task.
You can’t just go up to another car company and ask them for the details on all their steering gears to see which one might work for you. No one’s going to even answer the phone. You can leave a message but don’t expect to hear back from them.
The answer was to work through the suppliers. Fortunately, ZF-Lenksysteme, a well-known German steering supplier, agreed to work with us as long as we were able to find something in their current production catalog that would suit us.
The first step in this process was to determine what we actually needed. We did this by designing a front suspension while pretending that we could get whatever we wanted. We created a front suspension design we liked, and which would fit in our car. Out of that process came two very important numbers – the length of the steering rack, and something called the C-factor.
What We Were Looking For: Rack Length
View this post on Instagram
The length of the rack is the distance between the left and right inner tie rod joints. This dimension is fixed by the length of the rack bar and by the design of the steering gear housing and would require a complete redesign of the steering gear in order to change.
The reason this dimension is so important is that the position of the inner tie rod joint relative to the upper and lower control arm inner bushings establishes how the wheel will steer as the suspension moves up and down (the inner tie rod swings up and down, and so does the control arm; the difference in the arcs at the end of those “swings” has huge handling implications; this phenomenon is called “roll steer.”). If the rack length is too long, i.e., the position of the inner tie rod ends is too far outboard, then the length of the tie rods will be too short relative to the control arms and in the suspension shown above, the wheels will steer inward (toe in) as they move up or down. The opposite will happen if the rack is too short and the inner tie rod ends are too far inboard.
Of course, the vertical and fore/aft position of the inner tie rod are also very important to the proper functioning of the suspension, but this can be easily changed by moving the entire steering gear up/down or fore/aft. There is no way to modify the inboard/outboard position of the inner tie rod joint once the length of the steering gear has been established.
C-Factor
The other dimension that is critical to the function of the steering rack is called the C-factor, and it refers to the distance the rack travels during one full revolution of the steering wheel. This number is usually in the 45-65 mm/rev range, and it determines how fast the steering feels. A higher number means the rack moves more for each turn of the wheel and so the steering will feel quicker than if the C-factor is a lower number.
The C-factor needed for a specific steering gear is determined by an analysis of the overall steering ratio, which is the ratio between the degrees of steering wheel rotation compared to the degrees of steering at the front wheels. For most passenger cars, this number is on the order of 14-17:1, meaning for every 14-17 degrees the steering wheel turns, the front wheels will steer 1 degree.
We Found A Land Rover Rack That Would Work, But It Was Right-Hand Drive. So We Flipped It
Once we had established what steering gear we wanted, it was then a matter of seeing what was in production that might be close. We provided our requirements to ZF-Lenksysteme, and they quickly determined that a rack they were soon to put into production for the Land Rover Evoque was very close. Here’s the Evoque right-hand-drive rack:
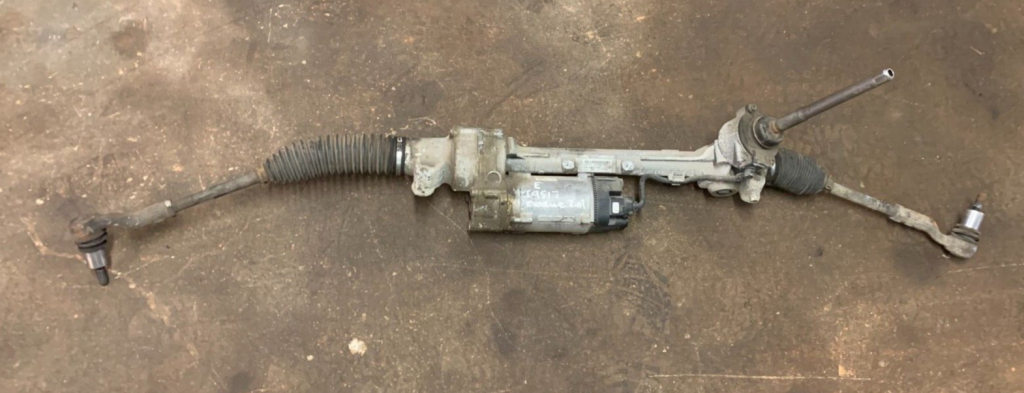
And here is a rack from a Model S:
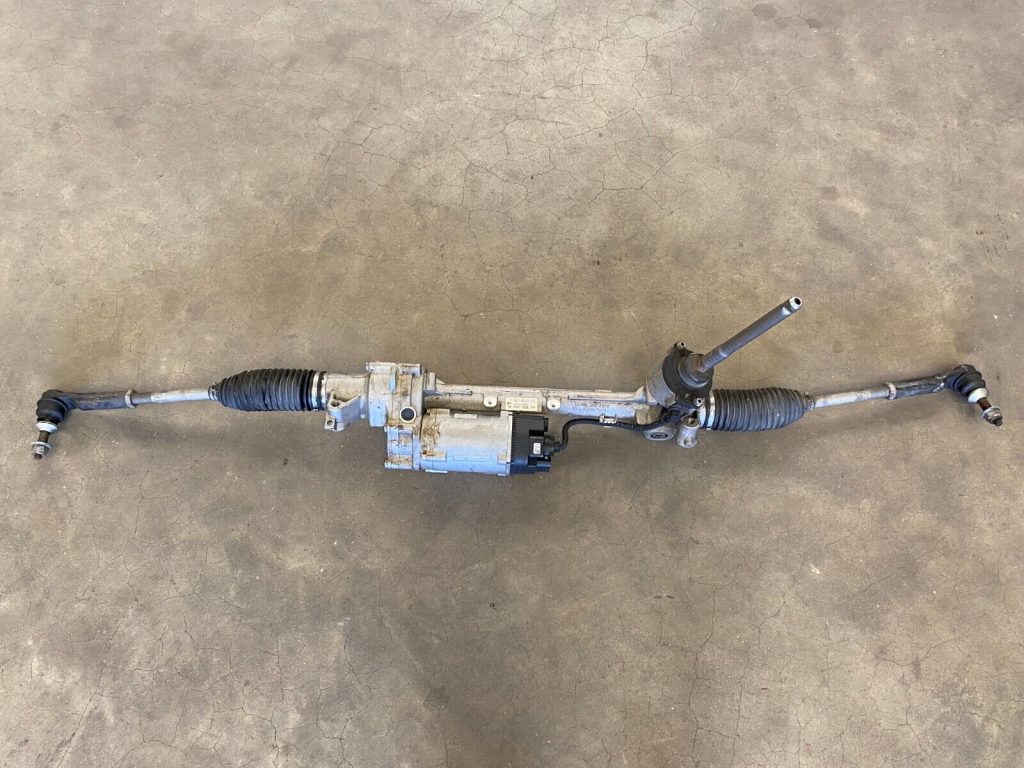
You can see how they are identical except for the ends of the tie rods (these are fairly cheap to tool), which had to be different to connect with our knuckle.
We would have to do some minor modifications to our suspension design to make it fit, but these would be easy to do and wouldn’t compromise the functionality of our design. The biggest problem was that the Land Rover gear was designed to be placed behind the centerline of the axle (called “rear steer,” not to be confused with rear axle steer) while we wanted to place ours ahead of the axle centerline (called “front steer”). The problem is that gears designed to be placed in front or behind the axle move in opposite directions. In a rack designed for front steer, the rack will move to the right when you turn the wheel to the right while in a rack designed for rear steer, the rack will move to the left when you turn the wheel to the right.
Clearly, we couldn’t simply take the Land Rover rack and place it into our suspension design. The car would steer to the left when you turned the wheel to the right!
Our solution was to use the right-hand drive rack from the Land Rover, flip it upside down (so the right side was now on the left and vice versa, and the bottom mounts that normally attach to the subframe are now pointing up), and place it in front of our axle for our left-hand drive application. Flipping the rack had the effect of reversing the direction the rack would travel, meaning it would now move in the correct direction when you turned the wheel and it also had the effect of moving the pinion, where the steering wheel and column attach, from the right side to the left side of the vehicle. This turned the Land Rover right-hand drive rear steer rack into a left-hand drive front steer rack that we could use.
That left only two things for us to do, or so we thought.
The first was to figure out how to attach the rack to our vehicle structure. Flipping the rack over meant that the bolts that mounted the rack would now end up on the top side of the housing and far away from our structure. The solution was to add two towers to the front subframe that reached up high enough to get to the bolts.
The second thing left to do was negotiate a commercial arrangement with Land Rover that would allow them to agree to let us use the steering gear they paid for, made with the tooling they purchased. Fortunately, we had some excellent negotiators on our team, and we came to a mutually beneficial agreement.
Another Problem: The Land Rover’s Steering Rack Was Too ‘Quick’
While the length of the Evoque rack was close enough that we could use it, the C-factor was quite a bit higher than we wanted. We knew we might have an issue, but we thought we could probably live with it. When we built our first prototypes however, we quickly discovered that the steering was much too quick.
The car was darty and difficult to drive on the highway. It wasn’t relaxing at all and would be uncomfortable for our customers. Since changing the C-factor of the rack meant designing and tooling a new rack bar and pinion, we had to find another way of making the steering feel slower. Our solution was to change the roll understeer of the front suspension.
How Clever Engineering ‘Canceled’ Out The Land Rover’s Overly-Quick Steering Rack
Roll understeer (which David describes in the Instagram video above) is a characteristic of a suspension design that forces the wheels to steer in the direction opposite to the steering input when the vehicle body rolls in a turn. In most cars, both the front and rear suspensions are designed to have some nominal amount of roll understeer. Here is how it works.
Let’s say we are making a left turn. We turn the steering wheel to the left which turns the front wheels to the left. As the vehicle enters the turn, the body will roll to the right which moves the right-side suspension slightly upward and the left side slightly downward. As the right-side suspension moves up, the roll understeer forces the right front wheel to steer slightly to the right, effectively subtracting some of the steering we put in at the steering wheel. The suspension actually steers a small amount less than we asked for. It “under” steers a little.
The amount of steering we get as the body rolls is controlled by the suspension design. Let’s take an example front suspension:
When viewed from the front:
you can see the upper and lower control arms as well as the tie rod and, in each case, the arcs each will trace as the suspension moves up and down. In this design, the arcs are all very similar, so the three arms will move relatively parallel to each other. But what if we moved the outer tie rod end down like this?
Now we see that the arc the outer tie rod end follows as the wheel moves up and down is tilted relative to the upper and lower ball joint arcs. This means that as the wheel moves up, the outer tie rod end will move outward (i.e it will “extend”) while the upper and lower ball joints are just moving more or less straight up. Since the steering rack and tire rod are mounted in front of the axle centerline in this design, the effect will be to steer the wheel outward as it moves up and inward as it moves down.
By moving the outer tie rod end down, we have changed the way the wheel steers as it moves up and down. By varying the amount we move the outer tie rod up or down relative to the upper and lower ball joints, we can change the amount of steer we get during wheel movement. This is how we change the amount of roll understeer our suspension has.
And that is exactly what we did on the original Model S. We moved the outer tie rod down in order to increase the amount of roll understeer. Effectively, we used the roll of the body during a turn to subtract from the amount of steering we asked for at the steering wheel which had the effect of slowing the steering down to a level we felt would be acceptable to our customers.
Saving Money By Flipping Control Arms, Smart Manufacturing
Using an existing steering gear wasn’t the only we tried to save cost in the Model S suspension. One of the most expensive parts of a suspension design are the tools needed to make the control arms, especially if those parts are forged. Forging tools can cost many hundreds of thousands of dollars depending on how complex the part is. If we can use fewer tools, then the total bill will be that much lower. An easy way to do this is to use try to use common parts on the left and right side. That way, you need a single tool where you otherwise would have needed two. In many cases this just isn’t possible. A knuckle, for example, is almost impossible to make the same on the left and right side. I’ve seen it done but in my opinion it seriously compromises the design.
But in other cases, it can be done. The lateral link in the Model S front suspension is a good example. This part is the same on both the left and right sides.
The rear suspension is where we were able to really put this philosophy to good use. While the rear knuckles are unique left to right, all the other suspension parts are common. Even the big lower link is the same left and right. The left side is simply the right-side part flipped over.
This link is actually quite complex since it is a hollow casting. Hollow castings use a sand core placed inside a steel mold leaving a small gap all around the edges where the molten aluminum is poured. Once the aluminum solidifies and the part is removed from the mold, the sand is trapped inside the part. It is then removed by shaking it violently so the sand falls apart and is poured out through a large hole left for that purpose. Once all the sand is gone, the hole is plugged or in some cases simply left open.
The knuckles are standard aluminum castings, nothing special there, but the other links were made in a way that also saved us a lot of money. They are extrusions.
This video does a good job of explaining what extrusions are and how they are made:
I mentioned earlier that forging tools are extremely expensive and while tools to make aluminum castings are a lot cheaper, they are still quite expensive. Extrusion tools, by comparison, are extremely cheap. The die to make the small integral link only cost a few thousand dollars while the die to make the upper link was on the order of 3-4 times that much. And since each of these parts is common on the left and right sides, it meant one set of dies for both sides of the suspension. A significant savings.
Using Common Parts Left-Right And Borrowing The Land Rover Rack Was Important
It may seem counter-intuitive to think that a car as expensive as the Tesla Model S would require us to be so concerned about cost, but when you are a start-up company with limited funds, every penny counts. The Model S was and remains an expensive car, so its functionality had to be at a commensurately high level. Achieving that with the suspension meant getting creative and saving cost wherever we could while still delivering the performance. It was a fun challenge.
I have mixed feelings when I see and read this. I see they compensated a flaw in the steering rack by changing the suspension geometry which should have been solved in the steering rack. If the car is unloaded and the suspension does not compensate for the higher turn rate then what?
Second I feel all this copying and ‘re-using’ looks good on paper to save money but isn’t this what we think China is doing all the time ? Taking the R&D from Western companies and then blaming that they copy it (and sometimes copy it badly, or improve it but not enough to call it innovation).
Please also do understand why some parts in a car are forged vs extruded ; forging is often stronger.
So this bragging about saving money has a hidden message ; this part is weaker than if we’d actually did it the ‘right’ way.
Wow, that rear suspension looks almost identical to the BMW E39 rear suspension.
It isn’t but the E39 certainly served as inspiration for it.
Hey! I just wanted to say I hope you add subtitles to your YouTube videos in the future. Given that they’re educational, you might also look into putting them on Nebula!
Yawn. Automotive engineers have been doing this long before Tesla but not surprising a former employee publishes an article like they were the first. Next.
I don’t think there was any part where he claimed to be the first.
This was simply an interesting insight from a perspective we don’t often get to hear from.
I’m sure that similar practices have been happening for a long time, but I certainly don’t see other articles out there as well written as this one on the topic.
Something doesn’t have to be the first to be worth writing about.
I wonder what percentage of automotive engineers ever do maintenance and repair work on the vehicles they engineer. I suppose easy assembly on the line has a higher priority over easy disassembly of subsystems (like lower A-arms on Sienna minivans, for example) or access to service items.
Then there’s stuff like the Chevy pickup I had in the early 70s. It came with a bottle jack, but if a front tire was flat (way out in the wilds of northern Saskatchewan, for example) the jack couldn’t fit under the specified jacking point — the lower A-arm (which was probably not identical to the one on the other side). Fortunately, I was on a dirt road and could dig a hole for the jack to sit in. After it was all done I wanted to drive directly to GM HQ, find the ones responsible for the jack fiasco, and beat them with my tire iron.