One of the greatest parts of the human experience is that everyone is perfectly imperfect. Yes, even you are imperfect. Besides, a world full of perfect people would be boring, or a Zack Snyder film. Because we’re imperfect, humans can be prone to making downright silly mistakes, and that can translate directly to wrenching. Screwing up while wrenching can cost you time, money, or even your safety. So, what was your dumbest mistake while wrenching? How much pain have you caused yourself fixing a car?
Admittedly, I have a bunch of stories of screwing up with cars. There was the time when the return line nipple on the gas tank of my doorless Ford Festiva broke during an off-road rally. I didn’t know that I could have just blocked off the return line, and instead, I attempted a wild trail repair. I crafted a new return line nipple out of duct tape, 50cc scooter fuel hose, and J-B Weld. It looked gnarly and was probably all kinds of unsafe, but it stopped the leak, at least long enough for the car to die in an off-road park.
Take a look at my awful work:
It was a dumb mistake to attempt a repair like that on such a critical part of a vehicle, and it’s arguably not the dumbest thing I’ve done while wrenching.
In 2020, I traded a $500 Mercedes-Benz 240D sedan with a blown differential for a second-generation Ford Ranger with a crushed left radius arm. I’m smart enough to know when a job is beyond my skill or tools, and I farmed out the radius arm replacement to a shop. I did the trade for the truck because Sheryl and I needed a vehicle to drive across the country to participate in the original Gambler 500 run in Oregon.
This vehicle needed to drive about 5,000 miles all in one trip, so I did the right thing and replaced anything goofy.
My inspection revealed that after the radius arm was replaced, the Ranger needed new power steering lines, new front brakes, and new front bearings. That’s not a lot of work and I knocked it out in a weekend. The power steering lines put up a fight, but cutting them off with a steak knife made replacing them easier.
Bearings on an old truck like this are also super easy, barely an inconvenience. I did them while fitting new rotors and pads up front a few nights before leaving for the Gambler 500. I capped off what I thought was a job well done with sweet American Racing wheels with all-terrain tires. My sweet technically $500 Ford Ranger was ready to rock.
On my first test drive the night before our departure, I realized my first dumb mistake. See, this Ranger had the economical, yet gutless four-cylinder engine. It simply didn’t have the power to propel the truck faster than 60 mph with those big tires, and that was with the throttle pinned. But I had exactly no time to find replacement tires. I had to run the truck’s original tiny tires in the rear with some spare larger wheels up front.
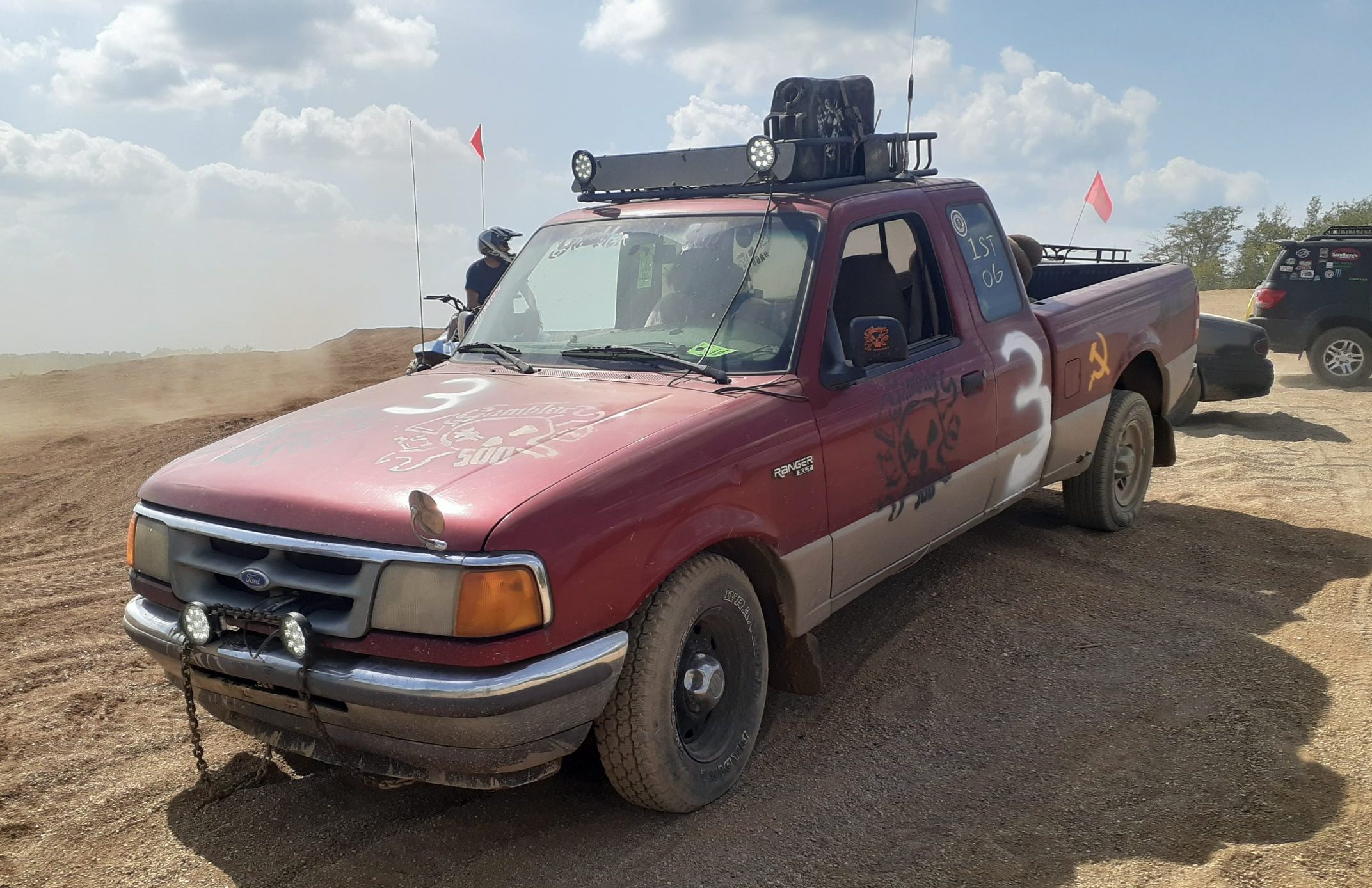
On the first day of our Gambler trip and about 200 miles in, I started hearing a weird scraping noise every time I applied the brakes. After about 250 miles, I decided to tell my friends, one of whom is a diesel mechanic, and we started looking over the truck. The problem was apparent the moment the front wheels were removed. One bolt securing the left brake caliper was missing while the other bolt was not even finger-tight. The slide bolt was also missing. The only thing that held the caliper in was the inside of the wheel and the fresh brake pads.
I could have sworn that I tightened those bolts, but I was also a few White Claws deep that night, so maybe I skipped that step and just put the wheels on. What I do know is that after we sourced the missing bolts and tightened everything down, it never happened again. I no longer drink while wrenching.
Have you done anything dumber? What was your silliest mistake while wrenching?
No, my driveway isn’t actually flat. Do not, not, put the front wheels on ramps if the rear wheels are not going to stay on the ground and blocked. I believe this lesson actually took two incidents to learn.
Mercedes, was that a Ryan George reference I saw?
When replacing the serpentine belt on my Prius I turned a 15 minute job (the serpentine belt only runs the water pump on this car, so it’s stupidly easy to replace) into a 2 day job by rounding off the nut that secures the tensioner. This nut is pretty notorious for being tighter than it should be based on the torque spec, and despite knowing that I made two big mistakes:
Fortunately, this is literally the first step in the process so I was able to just leave the old belt on there until I picked up two different types of rounded nut remover, the correct size breaker bar, and a replacement nut.
I also spent three nights replacing the bearings on my trailer, but that mostly because I lacked specific tools that were needed and didn’t find out until after all the stores were closed.
Cheap Harbor Freight piston ring compressor 🙁
Now I spend a little cash to get one thats specific to the diameter of the cylinder.
Cheap Harbor Freight spring compressor that broke, luckily the other one held and I got the top back on. They stopped selling those, BTW.
Assuming that ‘cleaning the throttle body’ on a modern Nissan would be the same as ‘cleaning the throttle body’ on, say, an ’92 F-150.
Throttle body spray hits the exposed electronics and gives you a Christmas tree on the dash for what you have done to the BCM.
Oh, and moving the valve by hand will just make it throw up its hands and quite altogether.
That was $700 I had to spend when I just wanted to clean out a TB….
Only variations on “be careful”.
My biggest self-inflicted wound on the matter was while replacing the windshield wiper switch/stalk on my Prius v. (Why? I had replaced my headlight switch previously with one with the fog light switch since adding fog lights, and that was a non-US variant with no words on it, and I wanted the matching windshield wiper stalk (~$50). Aesthetics!)
Okay, taking the steering wheel off! I did this once before with no issues, surely I can do it again without watching the same videos I did last time!…
Then I forgot to disconnect two little tabs before pulling. And something broke.
The piece that broke was very much a “oh wow, this would be a fascinating piece to learn about if it wasn’t that I just broke it and it’s going to cost a lot to fix!”
It was the clock spring, a.k.a. the part that allows you to still use steering wheel controls after the steering wheel has been rotated 500,000 times over the life of the vehicle or whatever. A really clever-looking piece of engineering with ribbon cables and rollers. And I had ripped the top cover off and was trying to reseat the ribbon cables by hand.
I got them back in good enough to fit and “feel” right, but the traction light came on and stayed on (among the codes thrown was “steering wheel position sensor”) and getting that replaced cost me $650+ for the part and more for labor at the dealership. At least it was a pleasant day, so the drive to the dealership was uneventful despite not having traction control.
Somewhat surprised that for something that significant, it didn’t also throw a check engine light, even if just to indicate “urgency.”
I was just lucky I had the money to burn at the time.
Wrenches are made for a reason and sometimes the reason is so you don’t do something silly. I had a weep at the oil pressure sending unit on my Grandville convertible. I was also freshly graduated from college and was looking at it in my parents’ driveway. My dad (who spent 20 years as a Pontiac tech) told me to get a line wrench and snug it a bit. I didn’t feel like digging out the wrenches so I got a pair of foot long channel locks and when I turned the unit, no, I didn’t wring off the threads on the sender. The extra torque of the pliers stripped the threads on the pot metal housing for the sender.
There was anger, tears (you’ve never seen my dad in a tirade about short cuts and not following directions). Following that part of the episode, we decided to put a bolt in and park the car until we could order a new housing. Luckily my brother showed up for dinner. He was an automotive machinist, and he happened to have a 400 on his bench waiting for dissassembly. He went over and fetched that housing and we put it all back together. You could say I also learned the old adage tighten until it strips, then back off a quarter turn.
I later paid my brother back. He had just done a 440 racing engine for his ‘Cuda. Just wouldn’t start. Cranked, had compression. So I said, let’s check for spark. Nothing. He was about to start throwing ignition parts at it and I said, could you have 180’d the distributor? Sure enough, that was the issue.
Make sure you know the cylinder #’s and firing order before yanking all the spark plug wires off the distributor.
That was a fun trial end error to get it right (this was before google).
I have 16″ forearms, the designers at Suzuki obviously did not. Just because it was in plain sight, didn’t mean I could get to it. And you can get fasteners off with your arm all contorted, but not start them.
If there is any type of hole in the ground near where you are working (sewer, lift pole holes, etc..) all fasteners will be drawn to it like a fucking magnet.
Chances are, whatever goes down the hole is the hardest/most expensive fastener to find at a parts counter….
If you’re installing a bolt that may be dropped into the nether, say like a Jeep CPS sensor bolt that is effectively unreachable if one only has regular arms with less than two elbows per, and which may fall into the bellhousing and lodge itself in the pressure plate, tie a short peice of fishing line to it. Tie the other end off so it will hold the fastener if it slips from your fingers. This way, if it’s dropped you are much more likely to retrieve it successfully. If all goes as planned, the little piece of fishing line should not affect torque spec or clamping force, and the pigtail can just be cut off.
Otherwise, always-always-always crack the fill plug before you open any drain plug or filter housing to make sure you’ll be able to refill after draining. Been there, wished-I’d-done-that on manual transmissions, diff plugs, 710 caps and have regretted it more than once before getting into the habit.
Support the engine if you’re gonna go around removing bolts from motor mounts. There’s a reason it really, really didn’t want to let loose, doofus.
I learned a ton ruining the Sentra though. 250k miles, 8 grand long since paid off? I got my money’s worth.
If you’re working in tight, largely inaccessible spaces, tie one end of a length of string to the part/tool, the other to your arm. You can easily cut it off later.
Learned this years ago after dropping a VW door lock clip down into the bottom of the door…but have since learned my lesson, including just a month ago installing a replacement cooling fan duct assembly on a Porsche.
I may have looked like a dork with a 10mm box wrench tied to my wrist, but made for zero drama when I eventually dropped it into the engine.
I used to do LOF on a scissor lift.
I was warned on my first day that the lift could only go so high, and had to be stopped manually.
One evening, sleep deprived, I raised the lift and neglected to release the button on time. A hydraulic line exploded and the lift smashed onto the locks.
In an effort to prevent having to get a rental for the customer until the lift could be repaired the next day, the foreman called all the mechanics around. They then proceeded to collectively try to lift the entire vehicle by hand, just enough to release the lock.
Thankfully, they failed, and no one died that night.
Everything about that story is bad clawing its way to worse. Glad nobody got hurt.
The difference between foot lbs. and inch lbs. was a painfully learned lesson when I was 15.
Don’t quickly do a brake job right after work & just before you go see a band.
-the sound of a brake pad installed backwards is something that will stay in your head for decades.
>no harm done except pride—and still made the first set, but still…
Pulled several wires off connectors under the hood of my Jensen Healey. Made some repairs only to realize no idea how to rewire the car. Melted many wires. Take a picture or more before you do anything.
Are you sure “melted many wires” isn’t still within spec?
Pretty sure considering the outcome.
All you did was speed up nature.
Oh god, even with pictures putting the Z4 harnesses back together took months. I eventually got it right but I still can’t tell you if passenger and driver are mirrored, rotated, or translated respective to one another. My shed was covered in increasingly desperate 8-pin wiring diagram drawings.
It doesn’t help that those sick bastards put two locking plastic tabs in a way that was literally inaccessible in the headlight assembly until I drilled holes.
Install nuts and bolts by hand as much as you can before you whip out the ratchet – and especially before using an impact gun. I’m the stubborn type, so I have left a lot of cross threaded bolts and studs in my wake over the years.
I even do it with lug nuts…I’d rather get my hands filthy/take a little more time than have that problem.
+1. If it’s already difficult start by hand, imagine how much harder it’ll be to back it off if you get it cross threaded. I will use a socket by hand for a little extra reach or alignment, but follow up with a few finger-lbs before using the ratchet or wrench.
When a tool is jammed, remove your face from the area before applying force. I hit myself in the face with a crowbar when it popped free and nearly pierced my botttom lip with a tooth.
Also look at where your hand gripping that wrench (even if force is being applied away from your face) is going to go when the bolt breaks loose/wrench slips off. Often, pushing that wrench with your palm is a good idea. That way you avoid stitches when your hand suddenly accelerates toward a body seam or castle nut.
As I read the first part of your comment, instead of knuckle busting, I was thinking of the multiple times a wrench has slipped and I full on punched myself in the face.
Oh, I did that several times myself. Then busted a couple knuckles wide open pushing away. Hoping someone can avoid my mistakes by taking this to heart.
I punched myself in the face a couple times. Just made me more rugged but it sure hurt.
I’ve done the same. At least that’s what they told me when I came to.
Most important lesson and the one I have ‘learned’ countless times from countless mistakes:
“If it looks, feels, or sounds weird or things are not happening as expected STOP and find out why.”
My first lesson in this was when I was in high school and also the day I found out older vehicles, especially trucks, often had left-hand threads on the left wheel studs. I broke all 16 off because I was to young and dumb to understand how little I actually knew about stuff…
If the bolt holding the caliper isn’t budging, don’t assume it’s just stuck and grab a breaker bar to really put some torque on it. I broke the bolt of because I was turning the wrong direction. My teenaged daughter was waiting for me to drive her somewhere in the afternoon but I just knew I’d get the brakes done before that. She ended up getting a ride from her Grandmother.
I would have just replaced the diff on the 240D.
It was a rust bucket hiding horrible Bondo rust hole patch jobs under equally an equally horrible truck bed liner paint job. In my final days with the car, the starter solenoid gave up on life, as did one of the connections to the accelerator pedal. Of course, rural parts stores didn’t have any of those parts. People placed bets on whether I was going to make it home given all of the issues.
As a final “F you,” the car’s sunroof got stuck open and the hood latch cable snapped, both on the day I traded it. Clearly, that car and I weren’t meant to have a good relationship. lol