Land speed racing is, to a degree, about power. The faster you go, the more power you need to overcome air resistance. Thus, the more power you have, the faster you can go with the appropriate gearing. Alternatively, you can cut air resistance and go faster with the same power. Most racers put effort into doing both.
Matt Brown is an automotive engineer, occasional Autopian contributor, and the YouTuber behind the channel SuperfastMatt. As you might guess by the name, he likes going fast, and he’s working to make his homebrew land speed racer faster than ever. To that end, he’s decided to design an aerodynamic body for his formerly bare-framed build.
Matt starts by outlining the basic factors that will influence his design. The car needs room for him inside, along with the wheels, a windscreen, an exhaust exit, and so on. He needs to allow for the basic functioning of the vehicle while creating a streamlined body that is as slippery and aerodynamic as possible.
The video explains the typical way to design a streamlined vehicle, wherein the nose is rounded off and the body tapered to a point at the rear. Indeed, allowing the air to come back together smoothly at the back of the vehicle is just as, if not more important than very gently punching a hole in it at the front of the vehicle.
In contrast, Matt’s land-speed car is nothing like that. It’s currently a bare frame, with plenty of protrusions from various components sticking out here and there, all contributing to a pretty poor drag figure.
To design his streamliner body, Matt decided to use a tool called AirShaper, with the company sponsoring the build. AirShaper is a tool for Computational Fluid Dynamics analysis, or CFD for short. Basically, it allows you to do digital simulations of airflow or water flow over an object, which can often be more convenient than building a scale model and using a wind tunnel. Performing meaningful CFD analysis is a highly technical skill that typically requires a great deal of advanced knowledge and experience to do well. Do it poorly, and your computational results will have little correlation with what happens in the real world.
The point of AirShaper is to make CFD more accessible than traditional packages which can have a very steep learning curve. As someone who took an introductory CFD course at university, I can easily understand the value there. Matt was also particularly lucky, with AirShaper CEO Wouter Remmerie also sitting in to provide his own insight on design.
Oh, and before we go further – here’s your crash course in aerodynamics. There are two kinds of drag of prime concern. There’s pressure drag, also known as form drag, which is caused by the shape of the object. It’s all about the pressure variation across the vehicle. Imagine a sphere traveling through the air. You’d see the air compressed as it impacts the front of the sphere. Meanwhile, as the air flows around the sphere, it creates a boundary layer, which then separates towards the back. This leaves a turbulent “wake” behind the sphere where there’s a low-pressure zone. This pressure differential creates drag, pushing the sphere back. Then, there’s friction drag, which is much simpler. It’s just down to the friction of air molecules on the surface of a vehicle.
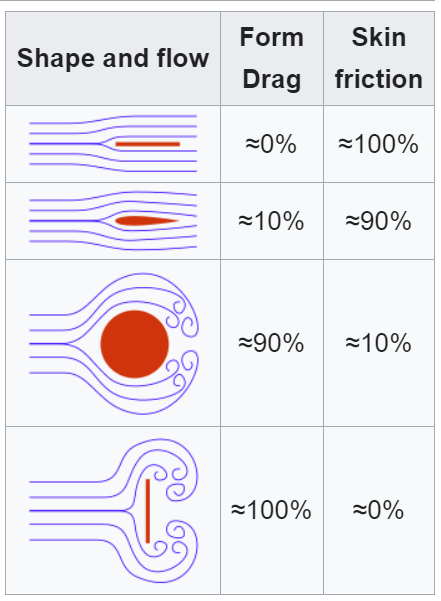
Matt ran his car at the Bonneville salt flats previously with no body, and used his results there as a verification for the figures he was getting out of AirShaper. The CFD analysis suggested his bare-framed design had a coefficient of drag (Cd) worse than an 18-wheeler, at 0.825. Total drag of the vehicle is much less, as the land speed car has a much lower frontal area, but it basically indicates that the vehicle is less aerodynamically efficient than a semi-truck.
Matt also noted the car was kind of unstable from his experience out on the salt flats. AirShaper similarly noted there wasn’t any aerodynamic force that would help keep it in a straight line—undesirable for a land speed car. Indeed, the car was so sketchy, he topped out at 157 mph according to his dash before backing off, though he suspected the car would actually be capable of closer to 180 mph with no body. AirShaper only accounts for aerodynamic resistance, and suggests the car would be capable of 180 mph with just 130 horsepower. Matt had the car dyno tested at 195 horsepower, but between things like rolling resistance on gooey salt and the loss of horsepower to altitude at Bonneville, he reckons the analysis was pretty much in the ballpark.
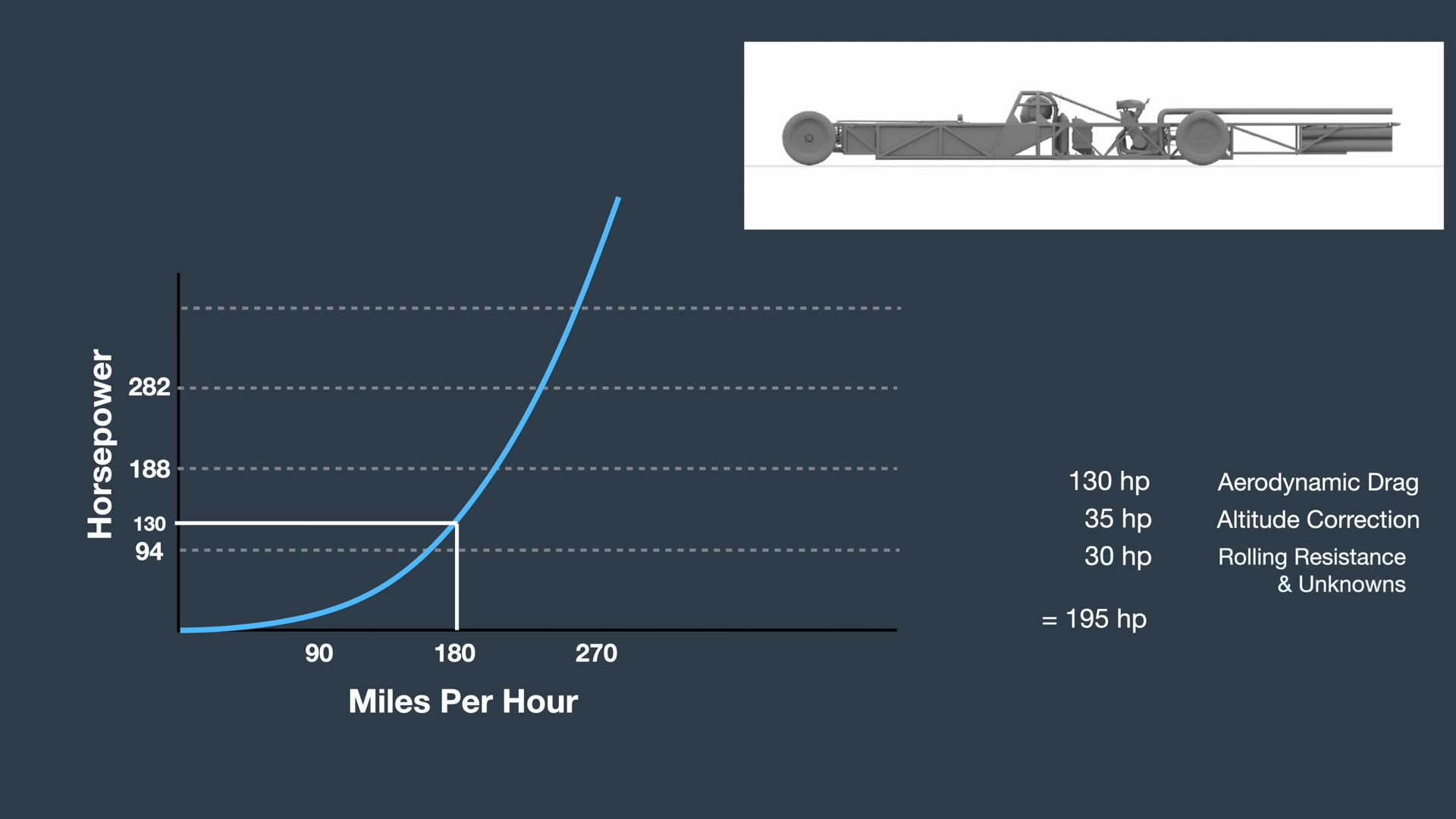
When designing the body, Matt started by keeping things simple where possible. He started by roughing out a design that’s round at the front and tapers towards the rear, leaving room for a driver, the engine, and the wheels. He noted the car was 22 inches wide to accommodate the front and rear wheels, and that there was little to gain from slimming the area between the two. That let him form the main lower body section from three flat panels, easing the job of constructing the body. He’s contemplating either doing that, or bending a large plastic piece into a single U-shaped panel that sits underneath the car.
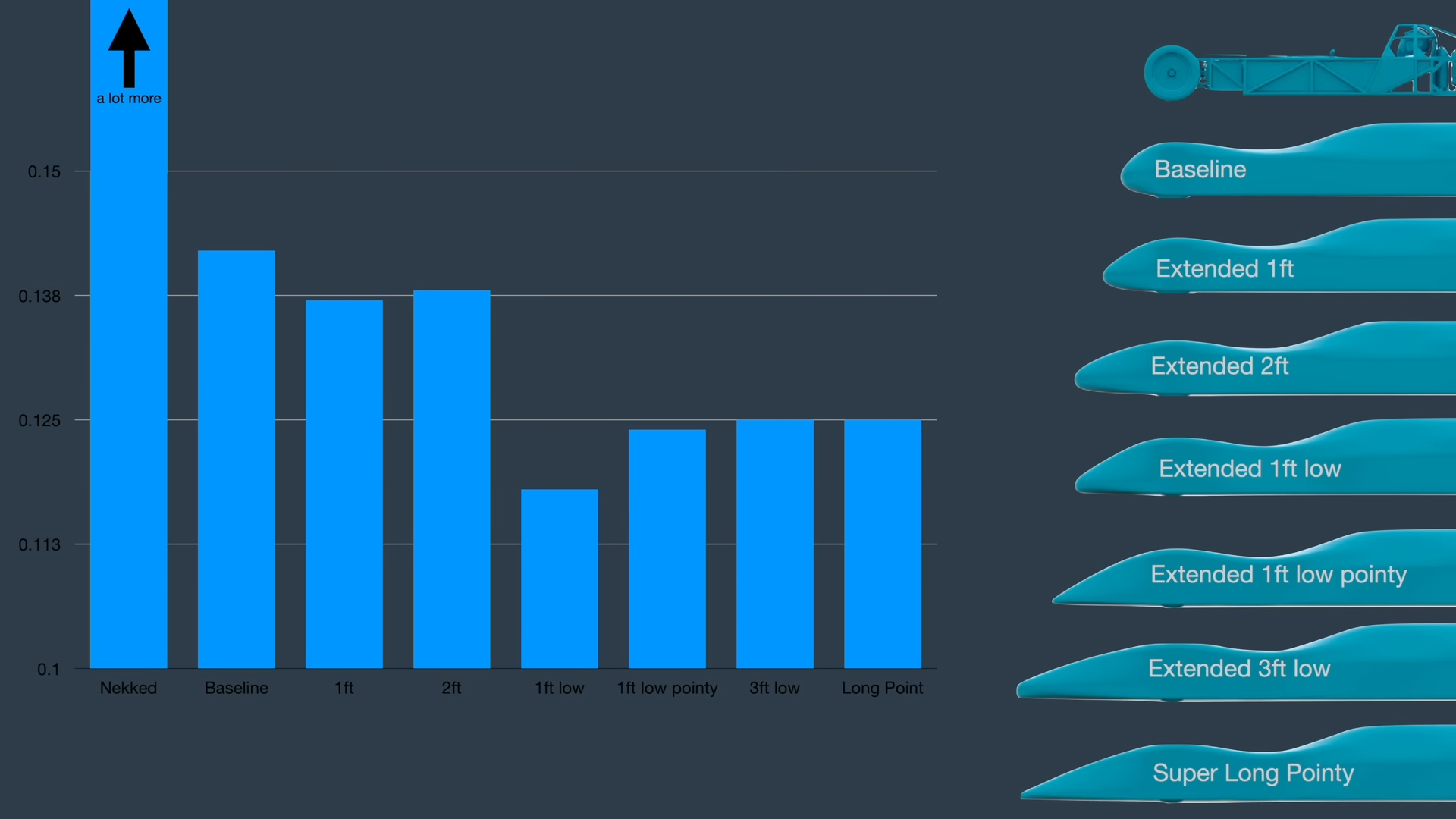
Matt then got into the meat of things, optimizing the nose to minimize the coefficient of drag. He set up AirShaper to simulate a vehicle moving along the ground. This configures the CFD analysis with the correct parameters for interactions between the ground and the vehicle itself. The AirShaper analysis kept finding that a long, lower nose offered lower drag. However, making it too long or too pointy didn’t really help. He now has to contemplate how to carve out a gap between the front wheels to allow better visibility without compromising drag.
At the back, Matt experimented by changing the angle at which the tail tapered together. He found that for his basic design, a longer, sleeker tail was worse. This was because while the subtler taper angle cut pressure drag by blending the air more gently, it added more friction drag from the greater surface area of this design. He ended up shortening the basic design until he found the point where the drag figures stopped improving.
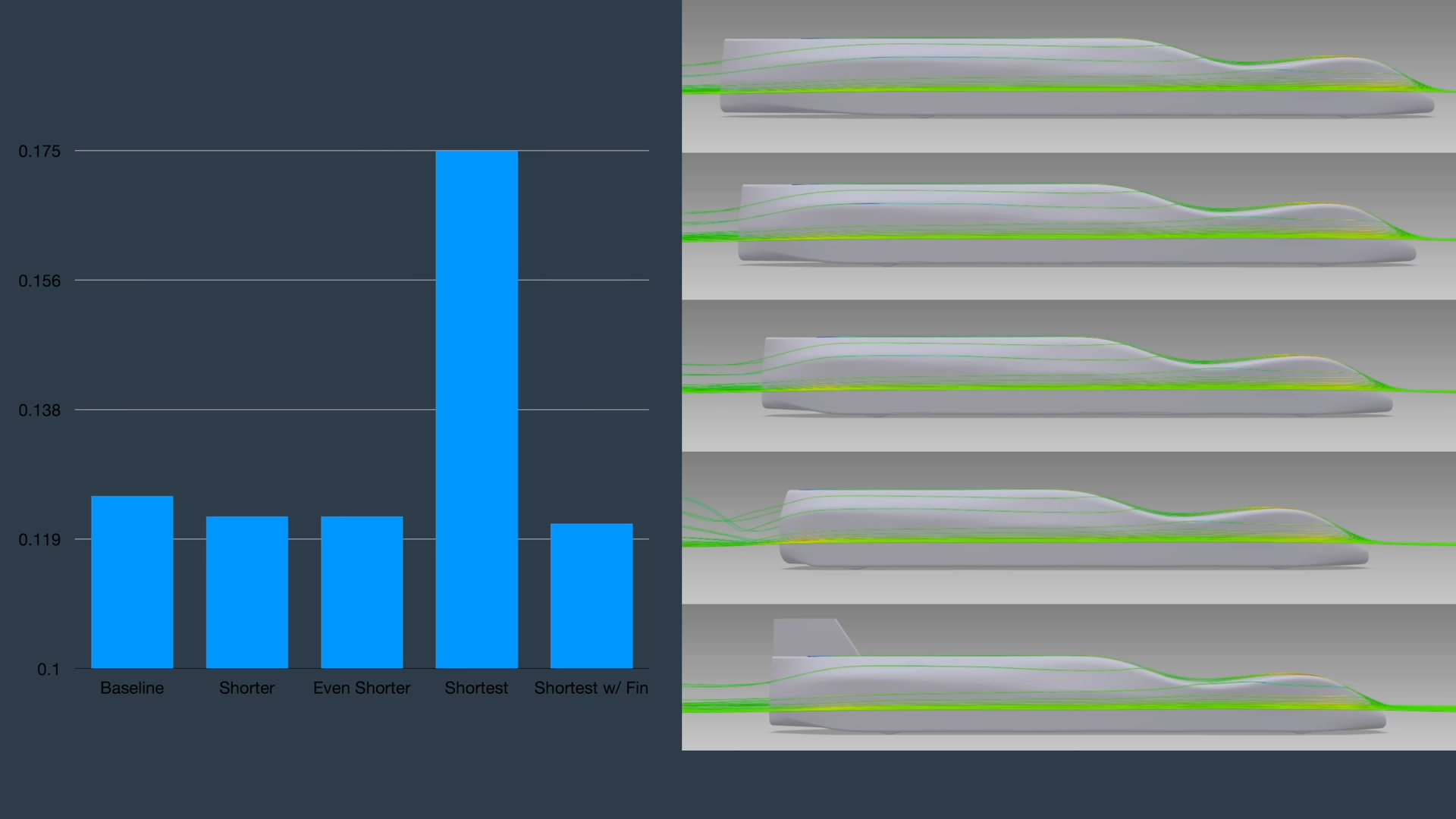
As for stability, Matt wanted the body to help keep the car on the straight and narrow. This meant ensuring that the center of pressure was behind the center of gravity of the car. Basically, imagine the center of gravity is the balancing point where we can say the mass of an object acts. The center of pressure is the point where the sum of the pressure field on the car acts.
Finding the center of pressure is complicated, but basically, adding more drag at the rear of the car pulls it rearward. Matt achieved this by adding a fin to the back of the car. It’s the same principle behind the fletches on the back of an arrow, or the flights on the back of a dart. They shift the center of pressure rearward, behind the center of gravity, providing aerodynamic stability in motion.
Adding the fin does add some drag, as it increases frontal area. However, by making it fairly small and giving it a streamlined teardrop shape, it keeps the additional drag to a minimum, both in friction drag and pressure drag respectively.
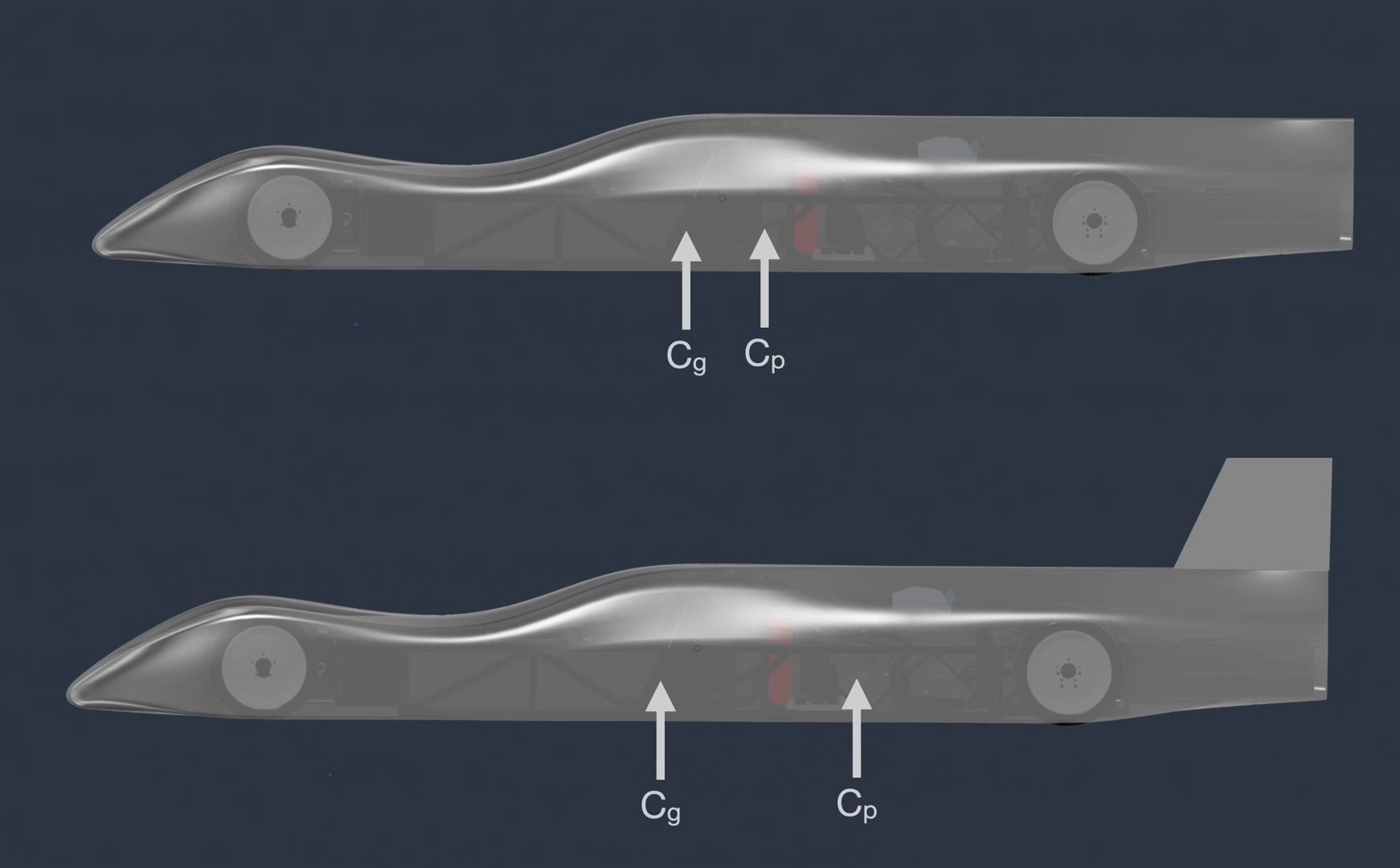
Matt then put together a rough top speed estimate for the car, based on similar rolling resistance and altitude losses as his prior bare-framed run at Bonneville. He reckons, even running the car on two cylinders rather than four, that it will be much faster than his previous run with the streamlined body installed. He estimates a top speed of 265 mph in that configuration. Running full power, just like his previous run, his calculations expect a top speed of 325 mph.
These figures are all very rough. They’re based on a great deal of assumptions and back-of-the-envelope extrapolations. However, it provides a vague idea of just how much impact the streamliner body could have. Yes, it’s a hugely significant gain in top speed, but that’s what you get when you slash your Cd from 0.825 down to 0.12.
Construction will pose some challenges. Matt has to figure out how to build the majority of the design in fiberglass. Plus, real-world considerations like fasteners and cutouts for wheels and the like will hurt efficiency. But regardless, Matt should expect to go much faster when he returns to the salt with a new streamlined body of his own design. We can’t wait to see how the real world results measure up against the simulations.
Image credits: Superfast Matt via YouTube Screenshot, Drag diagram credit to BoH, CC BY-SA 3.0
Interesting that the sphere is that un-aerodynamic. I suspect most people would not guess that intuitively (I wouldn’t anyway).
It depends on what speed the sphere is moving at relative to the air to determine how aerodynamically slippery it is, as well. The Cd of a sphere will decrease toward that of an airfoil as speed increases.
https://www1.grc.nasa.gov/beginners-guide-to-aeronautics/drag-of-a-sphere/
It also depends how rough the surface of the sphere is and whether its rotating. Ask any golfer.
The dimples in the golf ball are there to reduce skin friction. The speed of a golf ball is so low that the drag coefficient remains high, but the ball rotating could have the dimples also function as vortex generators that prevent as large of a wake from forming behind the golf ball as it would have without the dimples.
Also, consider the following experiment in aerodynamics on a Ford Taurus:
https://www.myscorecard.com/blog/?p=1278
Went from 26 mpg stock without dimples, to 29 mpg with dimples. I think in this case the dimples are also acting as vortex generators in addition to reducing skin friction. Skin friction is such a marginal amount of drag on a vehicle with a Cd ~0.30 that eliminating it alone won’t have that big a difference(skin friction on a sedan with a Cd in the 0.3 range is about 6% of the vehicle’s overall drag). A shape with a Cd of 0.3 is already sufficiently poor that vortex generators starting at the middle of the car could actually make a significant difference in drag.
On an inherently more slippery shape, dimples will most likely increase drag.
Right. The rotation and surface roughness determines how well that sphere mimics an airfoil.
I’d like to see a dimpled production car now. Especially SUVs and Trucks. Easy gains?
It’s bad enough that a dented or scratched up sphere is a significant improvement.
Checks to see if Toecutter has commented.
Leaves satisfied. Never let me down, buddy,
I’m obsessed with fuel economy, so articles pertaining to or which are adjacent to the subject will draw me in like shit does to flies.
Really? You’ve never mentioned it 😛
I’d flat undertray my cars for the fun of it if BMW hadn’t already done it for me.
Not gonna lie, I was disappointed this wasn’t a Matt Brown article. I like his writing.
I thought it was interesting when you talked about pressure drag/form drag and friction drag.
I have always heard those called shape drag and skin drag/surface drag. I think these terms are much more intuitive. Is the difference an Australian dialect thing?
My education is from textbooks, a university degree, and websites the world over. Everyone uses all different words for the same things all over the world in my experience, I’m not aware of an Australian form! But those in the industry might tell you there’s a more typical lingo down here.
I prefer “friction drag” or “skin friction” drag myself.
Fascinating read! Hopefully there’ll be a good number of follow-up posts on this project, looking forward to that!
This passage, “It’s currently a bare frame, with plenty of protrusions from various components sticking out here and there, all contributing to a pretty poor drag figure,” is reminiscient of some of the VW-Porsche race cars built and raced by Otto Mathé in the late 40s throughout the 50s; here’s one such car which looks like Mathé just draped a sheet of aluminium over a bare chassis and engine:
https://prototyp-hamburg.de/wp-content/uploads/2018/06/Otto-Mathe-Fetzenflieger-Copyright-Automuseum-Prototyp-1024×684.jpg
Mathé was so successful and beat the Porsche factory teams so frequently that Porsche refused to sell him any more engines; he had to procure engines through third parties. Yet Porsche included his wins in the total victories cited in their advertising for their race engines, ha. Remarkably, Mathé did all of this with a paralyzed right arm (caused by a motorcycle crash in the 20s or 30s) which required relocating the shift stick to the left side; while racing he would lean forward to press his torso on the steering wheel to hold it while he shifted with his left hand (and this was with unsynchronized gears, no less.)
Here’s another one of Mathé’s race cars with interesting aerodynamics: https://upload.wikimedia.org/wikipedia/commons/e/e9/VW_Typ_60_K_10_-_Porsche_Typ_64_%28Berlin-Rom-Wagen%29%2C_Bj.1939.jpg?20060921083815
Always enjoy updates on Matts site. His practical engineering solutions and dry humor always bring smiles.
One of the reasons the extended 1ft low nose works is because the non-low noses allow more of the airflow to be directed to the underside of the vehicle, where the ground moving relative to the vehicle underneath creates turbulence.
The longer low noses add skin friction and are probably no longer shaped appropriately for whatever rear shape the vehicle had, which would have to be adjusted to match the front. Hence why they showed higher drag. It might b possible that with an optimized rear shape, the longer noses could allow even lower drag than the one chosen with its rear.
This is a really cool article and I look forward to more.
Excellent insight! I really wish I’d taken my aerospace degree into motorsport sometimes.
It’s never too late for that.
I don’t even have an aerospace degree. I do have an electrical engineering degree though, and have read plenty of literature on ground vehicle aerodynamics. I’ve built custom electric vehicles that put the efficiency of any car you can buy to shame, exceeding their efficiency by 2 orders of magnitude.
Hoping one day to get my own shop space and build/sell something truly unique: a combination of inexpensive to buy, low maintenance, inexpensive to repair, repairable with basic tools, nearly free fueling costs, and acceleration to match a hypercar.
Matt also learned all about salt and how it gets …everywhere…and instantly corrodes things.
I felt bad for him dealing with all that rust after driving on the salt lake. Then I took my truck to Death Valley over New Years, drove to Devil’s Golf Course (a bit salt flat) the day after it rained, driving through puddles, and now I have about 5 year’s worth of rust on my exhaust which I’m kinda pissed about.
You should see all the rat rod guys in utah after speed week, they run around with all the caked on salt all over the cars until it flakes off naturally. It like a badge of honor or something. When I last went back to the flats with my dad it was very sticky, much like what Matt dealt with, so it made trying to drive back to his house a bit of an adventure with the shitbox focus I was driving at the time. Someday I’ll make it back and take my kidlets to see it. There’s no type of racing I’ve ever been party to quite like land speed stuff.
Yes that is a wonderful series he’s making on that one. Among all his other projects 😉
Did he sell/drop/forget the Teslaguar? It wasn’t on the latest “fleet update”
Uhh……. On the latest fleet update you’re talking about, he discussed the Jag and threw around the idea of selling it.
Alright thanks, just saw something this week, where he mentioned “all” the projects, without including that one 🙂
—–